High-vacuum technology is pivotal in achieving precise and efficient industrial processes, providing an environment where gas molecules are minimized to enhance performance. This technology is key in industries where even the slightest contamination can compromise product quality or process reliability.
At Orange Coast Pneumatics, we understand the critical nature of High Vacuum in industrial and commercial operations. Our commitment is to offer you top-tier equipment and accessories, ensuring your operations are not just effective but also cost-efficient.
Understanding High Vacuum
What is High Vacuum?
High Vacuum, in the context of industrial and scientific applications, refers to a condition where the pressure is significantly lower than atmospheric pressure, specifically within a range that goes beyond what mechanical pumps can achieve alone. This state is characterized by a paucity of gas molecules, resulting in minimal collisions between these molecules.
- Pressure Range: High Vacuum typically operates in a pressure range between 10−310−3 and 10−710−7 Torr (Torr is a unit of pressure). This range is significantly lower than the atmospheric pressure, which is about 760 Torr at sea level.
- Gas Molecule Density: In this vacuum level, the density of gas molecules is so low that they travel large distances without colliding with each other. This means the free path of molecules is a critical factor in processes that require minimal interference from gas molecules.
High Vacuum vs. Ultra-High Vacuum
Understanding the difference between High Vacuum and Ultra-High Vacuum (UHV) is crucial, as each serves different purposes and requires distinct technologies to achieve and maintain.
- Ultra-High Vacuum Range: UHV is achieved at pressures lower than 10−710−7 Torr. Reaching and maintaining UHV demands more sophisticated and sensitive equipment than High Vacuum. UHV is essential in fields like particle physics and nanotechnology, where even the slightest presence of gas molecules can interfere with experimental results or manufacturing processes.
- Technological Requirements: Achieving UHV often involves the use of specialized pumps, such as ion pumps or getter pumps, which are designed to operate efficiently at extremely low pressures. Additionally, the materials and design of the vacuum chambers must be meticulously controlled to reduce outgassing, which becomes a significant concern at these ultra-low pressures.
- Applications and Significance: While High Vacuum is sufficient for many industrial processes, UHV is required for operations where the utmost purity and absence of contamination are critical. Examples include the manufacture of semiconductors and the study of surface science, where even minute interactions with gas molecules can skew results or compromise product quality.
Importance in Industrial and Scientific Applications
High Vacuum plays a pivotal role in various industrial and scientific settings. Its applications range from electronic manufacturing, where it’s used in the deposition of thin films, to scientific research, where it’s essential for experiments in physics and chemistry that require controlled environments free from atmospheric gases.
- Enhanced Processes and Products: By reducing the presence of unwanted gas molecules, High Vacuum ensures that industrial processes are carried out with a higher degree of precision and purity. This leads to enhanced product quality, especially in sectors where even microscopic contaminants can be detrimental.
- Innovative Research and Development: In scientific research, High Vacuum allows for experiments and studies that would be impossible under normal atmospheric conditions, paving the way for groundbreaking discoveries and advancements in various fields.
Key Components of High Vacuum Systems
Vacuum Pumps: Types and Uses
The heart of any high vacuum system is the vacuum pump, a device designed to remove gas molecules from the vacuum chamber, thereby lowering the pressure. There are several types of vacuum pumps, each suited for specific applications and stages of vacuum creation.
- Rotary Vane Pumps: Often used as primary pumps, these are oil-sealed and ideal for reaching pressures up to the high vacuum range. They are widely used due to their reliability and relatively low cost.
- Turbo-molecular Pumps: These are secondary pumps, used in conjunction with primary pumps to achieve higher vacuum levels. They are particularly effective in ultra-high vacuum applications, commonly used in research and semiconductor manufacturing.
- Cryopumps: Utilizing extremely low temperatures to condense gas molecules, cryopumps are effective in achieving ultra-high vacuum. They are essential in applications where chemical reactions or contamination must be minimized.
Each type of pump has its unique advantages and operational requirements, making the choice of the right pump crucial for the efficiency and effectiveness of the high vacuum system.
Vacuum Chambers: Importance and Characteristics
Vacuum chambers are enclosed containers from which air and other gases are removed to create a vacuum. They are central to the functionality of high vacuum systems and come in various shapes and sizes, depending on their intended use. Key characteristics of vacuum chambers include:
- Material: Often made from stainless steel or aluminum, these materials are chosen for their durability and low gas permeability, essential for maintaining high vacuum conditions.
- Design: The design of a vacuum chamber must consider factors like size, shape, port configuration, and internal supports, all of which affect the chamber’s ability to maintain vacuum conditions and accommodate the necessary equipment or processes.
- Seals and Flanges: High-quality seals and flanges are crucial to prevent air leaks. Materials like copper and Viton are commonly used for their excellent sealing properties and resistance to vacuum conditions.
Low Vapor Pressure Materials
Materials with low vapor pressures are essential in high vacuum environments to minimize the release of gas molecules that can contaminate the vacuum. These materials are used in various components of the vacuum system, including seals, gaskets, and internal chamber coatings. They ensure that the surfaces within the vacuum chamber do not become sources of gas molecules that could compromise the vacuum integrity.
- Gaskets and Seals: Made from materials like Viton, PTFE (Teflon), and copper, these are designed to withstand the rigors of high vacuum conditions while providing effective sealing.
- Chamber Coatings: Special coatings are applied to the interior surfaces of vacuum chambers to reduce outgassing, a process where trapped gases are released from the chamber walls.
- Construction Materials: The choice of construction materials for vacuum system components is critical. Materials like stainless steel, which have low outgassing rates and high resistance to corrosion, are preferred.
Applications of High Vacuum in Industrial Settings
From semiconductor manufacturing to material sciences, High Vacuum is integral in a variety of applications. Its ability to maintain low vapor pressures is critical in processes where purity and precision are paramount, ensuring that production standards are not just met but exceeded.
Measuring and Maintaining High Vacuum
Tools like the cold cathode ionization gauge are essential in measuring and maintaining the right vacuum levels. It’s not just about creating a vacuum but ensuring its stability throughout your operation, a task that requires precision equipment and expertise.
The Science Behind High Vacuum
Understanding the science behind High Vacuum is crucial for leveraging its full potential. In these environments, gas molecules behave differently, adhering to principles of physics that differ significantly from normal atmospheric conditions. This section explores these unique behaviors and the scientific principles that make high vacuum environments so effective and necessary for precision work.
Innovations in High Vacuum Technology
Recent advancements in High Vacuum technology have opened up new possibilities across various industries. From more efficient vacuum pumps to advanced materials for vacuum chambers, these innovations not only enhance performance but also contribute to cost savings and operational efficiency. This section will highlight some of the most notable advancements and their implications for industrial applications.
High Vacuum Safety and Regulations
Working with High Vacuum systems involves adherence to stringent safety protocols and regulations. This section will outline the necessary safety measures and industry standards, ensuring that your operations not only benefit from high vacuum technology but also comply with all regulatory requirements.
Environmental Impact of High Vacuum Systems
High Vacuum systems, while crucial for many industrial processes, also have environmental considerations. This section will discuss the sustainability aspects of high vacuum technology, including energy consumption, material choices, and ways to minimize the environmental footprint of these systems.
Choosing the Right High Vacuum Equipment
Selecting the right equipment is crucial for maximizing the benefits of High Vacuum technology. This section will provide insights into choosing the best vacuum pumps and chambers and balancing factors like performance, durability, and cost-efficiency to meet your specific needs.
Maintenance and Troubleshooting of High Vacuum Systems
Maintaining the integrity of High Vacuum systems is key to uninterrupted operations. This section will offer guidance on regular maintenance routines and provide troubleshooting tips for common issues, ensuring that your high vacuum systems function optimally and reliably.
Conclusion
The benefits of High Vacuum in industrial and commercial settings are clear: enhanced precision, improved product quality, and increased operational efficiency. At Orange Coast Pneumatics, we stand ready to supply you with the superior-quality equipment and accessories your pneumatic systems need.
To elevate your operations with our Vacuum solutions, contact our team today. We’re here to guide you through every step, ensuring your success and satisfaction.
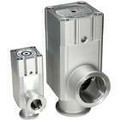
Angle and In-line Valves
High vacuum angle and in-line valves are for use in industrial applications employing high vacuum and process gases. Common industries that may use these angle valves include semiconductor, solar and other electonics production, as well as food and pharmaceutical manufacturing.

Slit Valves
Series XGT slit valve is suitable for the partition valve between the load lock chamber and the transfer chamber, and between the transfer chamber and the process chamber in semiconductor manufacturing equipment, etc.
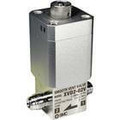
Smooth Vent
Smooth vent valve series XVD2 is a normally closed type valve with connection types VCR (male & female) and Swagelok. Port size for the main supply is 1/4" and orifice is 3mm. Materials consist of SUS316L (body & bellows), SUS304 (diaphragm) and FKM (valve and external seal).
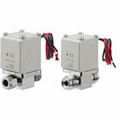
Solenoid Valve
Series XSA is a normally closed solenoid valve suitable for air or inert gas in high vacuum applications. This valve functions properly at an operating pressure as low as 1x10-6 Pa(absolute). Face Seal and compression fitting options offer extremely low levels of internal and external leakage. Two DC and eight AC voltage options are available, paired with multiple electrical entry styles.