When it comes to pneumatic systems, a reliable source of superior-quality components is vital. Among these components, pneumatic connectors play a crucial role in ensuring efficient and effective operations.
At Orange Coast Pneumatics, we offer an expansive selection of connectors for pneumatic systems. Find the best pneumatic connectors for your operations, here.
Then, continue reading to the purpose, applications, and benefits of pneumatic connectors, providing you with the information you need to make informed decisions for your industrial and commercial systems.
What is a Pneumatic Connector?
Pneumatic connectors are essential elements in pneumatic systems. These systems utilize compressed air or gas to power various mechanical processes, making them widely used in industries such as manufacturing, automotive, and automation.
A pneumatic coupling consists of two main parts: the socket and the nipple. The connector's design enables quick and secure connections between different pneumatic components, such as hoses, tubes, valves, and cylinders.
These components are designed to fit together securely, creating an airtight connection. The socket and nipple are typically equipped with internal seals, such as O-rings, to prevent leakage and ensure efficient operation of the pneumatic system.
What are Pneumatic Fittings Called?
Pneumatic fittings are also referred to as compressed air fittings. These fittings play a crucial role in connecting pneumatic tubes or hoses to various pneumatic components, such as valves, cylinders, and air tools.
They are available in a wide range of sizes, shapes, and configurations, making it possible to find the perfect fitting for every pneumatic tube. Pneumatic fittings provide a secure and leak-free connection.
They often feature quick-connect mechanisms, allowing for easy and efficient assembly and disassembly of the pneumatic system. These fittings are commonly made from materials like brass, stainless steel, or plastic, depending on the specific application requirements.
What are the Different Styles of Pneumatic Fittings?
- Barb Fittings
- Compression Fittings
- Push-in Fittings
- Quick Connect Fittings
- Threaded Fittings
Pneumatic fittings come in a variety of styles, each suited for different applications and installation methods. Understanding the different styles can help you choose the right fittings for your pneumatic systems.
Barb Fittings
Barb fittings have ridged ends that grip onto the inner diameter of a pneumatic tube. They are commonly used with flexible tubing and are ideal for low-pressure applications.
Compression Fittings
Compression fittings use a nut and ferrule system to create a tight seal. The nut is tightened, compressing the ferrule around the tube and forming a leak-free connection.
Push-in Fittings
These fittings feature a simple push-to-connect mechanism, allowing tubes to be inserted directly into the fitting. The built-in gripping mechanism ensures a secure connection without the need for additional tools.
Quick Connect Fittings
Quick connect fittings enable rapid assembly and disassembly of pneumatic systems. They feature a push-to-connect or snap-in mechanism, making it convenient to connect and disconnect tubing without the need for tools.
How Do Pneumatic Quick Connectors Work?
Quick connectors employ a simple yet effective mechanism for fast and secure connections. Inside the connector, there are spring-loaded valves that automatically engage and seal the connection when the nipple is inserted into the socket.
As the pressure increases inside the system, the valves further tighten the seal, ensuring a reliable connection. When it's time to disconnect, quick connectors feature a release mechanism that allows for effortless disconnection.
By pressing or pulling a release button or collar, the valves inside the connector are released, allowing the tubing to be easily disconnected without any leakage or loss of pressure.
Threaded Fittings
Threaded fittings have male and female threads that screw together to form a secure connection. They are suitable for high-pressure applications where a tight seal is required.
Find the Best Connectors for Your Systems at OC Pneumatics
At OC Pneumatics, we prioritize quality, offering connectors that meet the highest industry standards. Our connectors are manufactured with precision and undergo rigorous testing to ensure their durability, performance, and reliability in demanding pneumatic applications.
To find the best pneumatic connectors for your operations, reach out to our team today.
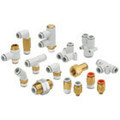
Fittings
For businesses that rely on pneumatic systems to run their operations, finding the right air connection fittings is essential. Poorly fitted components can lead to significant losses in efficiency and performance, as well as increased maintenance costs and downtime.
On the other hand, having high-quality pneumatic air fittings from a trusted manufacturer can improve system functioning and provide long-term savings. SMC USA provides an extensive selection of reliable pneumatic fittings for all types of applications.
At Orange Coast Pneumatics, we’re an authorized national elite distributor for SMC USA. Find the best air fitting connectors for your pneumatic systems below; then, continue reading to learn more about the SMC fittings catalog.
For businesses that rely on pneumatic systems to run their operations, finding the right air connection fittings is essential. Poorly fitted components can lead to significant losses in efficiency and performance, as well as increased maintenance costs and downtime.
On the other hand, having high-quality pneumatic air fittings from a trusted manufacturer can improve system functioning and provide long-term savings. SMC USA provides an extensive selection of reliable pneumatic fittings for all types of applications.
At Orange Coast Pneumatics, we’re an authorized national elite distributor for SMC USA. Find the best air fitting connectors for your pneumatic systems below; then, continue reading to learn more about the SMC fittings catalog.
SMC Pneumatic Fittings
SMC pneumatic fittings are an ideal choice for businesses that want a secure, fast and reliable connection for their pneumatic systems. With quality construction and advanced sealing technology, these fittings ensure that your operations run smoothly, regardless of the size of your operations.
SMC's push-to-connect fittings provide superior performance compared to traditional threaded connectors due to their simple one-piece construction and innovative design features. With these fittings, users can enjoy a secure connection with minimal leakage — ensuring that your system remains pressurized at all times.
For those looking for something more specialized, SMC USA offers specialty connectors designed with advanced packing material that seals tight under pressure without sacrificing flow rate. This provides you with the control you need to manage your system without having to worry about leaks or pressure drops.
One-Touch SMC Air Fittings
When it comes to pneumatic air fittings, SMC Corporation of America is the leading provider. SMC Push-to-Connect Fittings provide an easy, intuitive, and reliable solution for businesses that use pneumatic systems in their operations.
With one simple push, SMC push fittings create tight, secure connections that make installation and maintenance quick and painless. For applications where space is limited or access is difficult, SMC push-in fittings are ideal.
The compact design requires minimal force to install and ensures a secure connection without risk of leaks or wear and tear on pipes or hoses. Plus, the tubing can be removed with just the touch of a finger — making removal and replacement easier than ever before.
One-Touch Pneumatic Air Fitting Types
SMC one-touch tube fittings come in metric and inch-size pneumatic fittings and are available in a wide variety of sizes, body styles, and thread types. SMC offers one-touch pneumatic tubing fittings in a number of special environments, such as anti-static, flame-resistant, clean room, DOT, and food service settings.
Anti-Static Pneumatic Compression Fittings
Don’t let static electricity or other external conditions put a strain on your operations — turn to anti-static pneumatic compression fittings from SMC USA. These products are designed to meet the toughest industrial applications and provide reliable performance in any anti-static environment.
SMC DOT Fittings
Air brake fittings from SMC USA are designed to meet strict Department of Transportation (DOT) regulations. These DOT-compliant fittings are the perfect addition to any pneumatic system that needs to meet federal requirements.
SMC’s air brake fittings provide a secure and reliable connection that is tamper proof and meets all DOT requirements. These fittings are made with durable polyamide material, along with stainless steel threads for maximum strength and integrity.
Specialty SMC Connectors
For more demanding applications where reliability is a must, SMC offers specialty connectors. These are designed with packing that provides positive sealing under pressure without compromising flow rates like compression fittings often do.
These precision-engineered connectors are built to endure in high temperature and extreme pressure environments. This provides you with peace of mind when it comes to your pneumatic system operations.
One-Touch air fittings from SMC come with added benefits, including:
- Improved hygienic seals.
- Joint integrity, even in hazardous atmospheres.
- Reduced assembly time, eliminating costly downtime associated with traditional threaded connections.
Find the Best Pneumatic Connectors at Orange Coast Pneumatics
SMC fittings are the perfect solution for businesses who need to manage their pneumatic systems with ease. Whether you have a large or small operation, these air fittings offer quality and reliability at an affordable price.
So if you’re looking for dependable air fittings with superior performance and unbeatable value, you can’t go wrong with SMC USA. To find the best air connectors for your pneumatic systems, reach out to our team today.
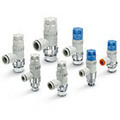
Speed Controllers
Speed control valves are vital for any business that utilizes pneumatic systems in their industrial or commercial operations. These essential components ensure precise control of the speed and direction of pneumatic actuators, which are used to control and move various components in the system.
At Orange Coast Pneumatics, we offer a diverse range of air-flow control valves from The SMC Corporation of America. Find the best solution for your business, here; then, continue reading to learn more about the purpose and benefits of pneumatic valve controllers.
What is Pneumatic Flow Control?
Pneumatic flow control is an essential aspect of the pneumatic system. It enables precise control of the speed and direction of pneumatic actuators. Specifically, it involves the use of flow control valves to regulate the flow of compressed air to and from pneumatic cylinders, motors, and other devices.
How Does a Pneumatic Speed Control Valve Work?
Pneumatic control valves work by controlling the rate at which air is allowed to flow through them.
These valves have an adjustable opening that can be adjusted to limit the flow of compressed air.
The valve is typically placed in the airline that leads to the pneumatic cylinder, and as the air flows through the valve, it is slowed down, which in turn slows down the speed of the cylinder.
What are the Four Main Types of Pneumatic Control Valves?
There are four main types of pneumatic control valves that are commonly used in pneumatic systems. These include:
- 2-Way Directional Control Valves
- 3-Way Directional Control Valves
- 4-Way Directional Control Valves
- Pneumatic Spring Offset Valves
2-Way Directional Control Valves
2-way directional control valves are used to regulate the flow of compressed air in a single direction. They can either be normally open or normally closed and are typically used in simple on/off applications.
3-Way Directional Control Valves
3-way directional control valves have three ports and are used to control the flow of compressed air to a pneumatic actuator. They can be either normally closed or normally open, and are commonly used in applications where the pneumatic actuator needs to be controlled in both directions.
4-Way Directional Control Valves
4-way directional control valves have four ports and are used to control the flow of compressed air to a pneumatic actuator that requires precise control of the direction of movement. They are typically used in applications where the pneumatic actuator needs to move in multiple directions.
Pneumatic Spring Offset Valves
Pneumatic spring offset valves refer to any valve that uses a spring to release the valve spool to return to its original position.
Pneumatic Cylinder Speed Control
It’s critical to have precise control of the speed and direction of pneumatic actuators in manufacturing and industrial applications. Without reliable flow control valves, you may experience issues such as equipment damage, decreased efficiency, and increased downtime.
SMC speed controllers have a broad range of applications, and some even boast a specialty focus, such as air cylinder speed control use at low speeds and with residual pressure. Further options within the series include a built-in one-touch fitting, an integrated pilot check valve, a meter-in and meter-out dual flow control, and a stainless steel option.
With the ASR series, the environmentally conscious consumer can reduce air consumption by 25% through the inclusion of a quick supply exhaust valve. Air cylinder speed control is easy with our comprehensive line of products.
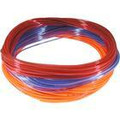
Tubing
Tubing is an essential component of pneumatic systems used in a wide range of industrial and commercial applications. They’re used to transport compressed air, which is used to power various pneumatic tools and machinery, such as valves, cylinders, and actuators.
Pneumatic tubing is made from a variety of materials, each with its unique properties that make it suitable for specific applications. In this article, the pneumatic systems experts at Orange Coast Pneumatics explore the purpose of tubing and the different types of air tubing available.
What is Pneumatic Tubing Used For?
Pneumatic tubing is used to transport compressed air in pneumatic systems. Compressed air is a reliable and efficient power source that is widely used in manufacturing, construction, and other industries.
Pneumatic tubing is essential for the operation of pneumatic systems. It enables your system to transport compressed air from the compressor to the various pneumatic tools and machinery.
Pneumatic tubing is used in a wide range of applications, such as:
- Manufacturing: Pneumatic tubing is used in manufacturing processes to power pneumatic tools and machinery, such as grinders, sanders, and drills.
- Automotive: Air tubing is used in automotive manufacturing to power pneumatic tools and machinery, such as impact wrenches and paint sprayers.
- Construction: Air tubing is used in construction to power pneumatic tools and machinery, such as nail guns and jackhammers.
- Food and Beverage: Pneumatic tubing is used in food and beverage production to power pneumatic machinery, such as filling machines and packaging machines.
- Medical: Pneumatic tubing is used in medical equipment, such as ventilators and anesthesia machines.
What are the Different Types of Pneumatic Air Tubing?
There are 8 primary types of air tubing for pneumatic systems. These include:
- Fluororesin Tubing
- Moisture Control Tubing
- Nylon Tubing
- Polyolefin Tubing
- Polyurethane Tubing
- Polyethylene Tubing
- Spark-Resistant Tubing
- Wear-Resistant Tubing
Fluororesin Tubing
Fluororesin tubing is a high-performance tubing that is resistant to chemicals, heat, and moisture. It is commonly used in applications where there is exposure to harsh chemicals or high temperatures.
Moisture Control Tubing
Moisture control tubing is designed to prevent moisture buildup in pneumatic systems. It is commonly used in applications where there is a risk of moisture contamination, such as in food and beverage production.
Nylon Pneumatic Tubing
Nylon pneumatic tubing is a flexible and lightweight tubing that is resistant to abrasion, corrosion, and chemicals. It is commonly used in applications where there is a need for flexibility and durability, such as in robotics and automation.
Polyolefin Tubing
Polyolefin tubing is a flexible and lightweight tubing that is resistant to chemicals and abrasion. It is commonly used in applications where there is a need for flexibility and durability, such as in automotive manufacturing.
Polyurethane Tubing
Polyurethane tubing is a flexible and lightweight tubing that is resistant to abrasion, chemicals, and kinks. It is commonly used in applications where there is a need for flexibility and durability, such as in pneumatic tools and machinery.
Polyethylene Tubing
Polyethylene tubing is a flexible and lightweight tubing that is resistant to chemicals, abrasion, and impact. It is commonly used in applications where there is a need for flexibility and durability, such as in food and beverage production.
Spark-Resistant Tubing
Spark-resistant tubing is designed to prevent static electricity buildup in pneumatic systems. It is commonly used in applications where there is a risk of explosion or fire, such as in oil and gas production.
Wear-Resistant Tubing
Wear-resistant tubing is designed to withstand wear and abrasion caused by friction, impact, and other mechanical forces. It is commonly used in applications where the tubing is exposed to heavy wear and tear, such as in mining, construction, and material handling.
SMC Tubing from Orange Coast Pneumatics
SMC manufactures fluororesin tubing for use in environments involving high temperatures and/or corrosive fluids. Pneumatic tubing is also available in a number of other materials both with and without reinforcement for use in standard applications.
SMC fittings incorporate a positive tube seal while the fitting is under pressure enabling you to use polyurethane tubing.
Air Tubing Sizes
Pneumatic tubing sizes include:
- 1/8"
- 5/32"
- 3/16"
- 1/4"
- 5/16"
- 3/8"
- 1/2"
Metric tubing sizes include:
- 3.2mm
- 4mm
- 6mm
- 8mm
- 10mm
- 12mm
- 16mm
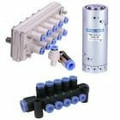
Manifolds
Manifolds allow multiple tubes to be connected or disconnected in a one touch operation without tube connection errors. The time required for connection and disconnection is substantially reduced.
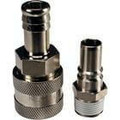
Quick Couplers
S coupler series KK employs a unique connection method. A slim body design and large effective area are achieved with a construction that does not use steel balls or valve springs and therefore does not restrict the flow path. Together with a reduction of the body size, pressing parts and resin parts are used to achieve an overall weight reduction.
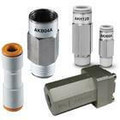
Check Valve
Air check valves are critical components in pneumatic systems. They regulate air flow to maintain the system's desired pressure levels, prevent backflow of fluids, and protect components from damage.
At Orange Coast Pneumatics, we offer a diverse range of air compressor parts from The SMC Corporation of America. SMC is a leading provider of pneumatic automation components that are designed to meet several industrial requirements.
Find the best one-way air valve for your pneumatic systems, here. Then, continue reading to learn about pneumatic check valves and their four, basic variations.
What is the Purpose of a Pneumatic Check Valve?
In a pneumatic system, compressed air flows through pipes and components. Any backflow or reverse flow of air can cause equipment failure, loss of pressure, or contamination of the system.
Pneumatic check valves act as a one-way valve to prevent backflow and protect the system from damage. They are used in various applications, including vacuum pumps, compressors, and pneumatic cylinders.
Simple check valves only permit flow in one direction, while pilot-operated check valves can permit reverse flow when released via a pilot signal. All SMC check valves feature low cracking pressure in the normal flow direction.
What are the Four Basic Types of Air Pump Check Valves?
The 4 most common types of air-flow check valve include:
- Ball Check Valves
- Diaphragm Check Valves
- Swing Check Valves
- Spring Check Valves
Ball Check Valves
This type of check valve has a ball that seals the opening, allowing the air to flow in only one direction. When the pressure in the pipe exceeds the pressure above the ball, it pushes the ball against the seat, closing the valve.
Diaphragm Check Valves
Diaphragm check valves have a flexible diaphragm that seals the valve opening. The pressure above the diaphragm keeps the valve closed until the pressure below the diaphragm exceeds the pressure above it, causing it to open.
Swing Check Valves
Swing check valves have a hinged disc that swings open to allow the air to flow in one direction. The disc swings back to its closed position when the pressure in the pipe drops below the pressure above it, preventing backflow.
Spring Check Valves
Spring check valves have a spring-loaded disc that seals the valve opening. The spring keeps the disc closed until the pressure above the disc exceeds the spring pressure, allowing the air to flow in one direction.
Air Compressor Check Valves from Orange Coast Pneumatics
SMC offers two types of check valves: standard check valves and pilot check valves. The main difference between the two types is that pilot check valves can reverse air flow after receiving a pilot signal.
SMC's standard check valves are available in various sizes and configurations, including threaded and push-to-connect fittings. They are compact, lightweight, and easy to install, making them an excellent choice for most applications.
SMC's pilot check valves enable reverse flow once they receive a signal from the pilot. They are ideal for use in applications where the valve is located in a hard-to-reach area or when precise
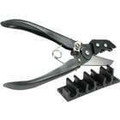
Accessories
Accessories like the TK tube cutter, tube stands and reels as well as the TG tube release tool makes installation and maintenance easier and more organized.